Peak Performance
As one of the largest and oldest producers in the western United States, CalPortland Company has irrevocably woven itself into American history with its rich, storied past. Established in 1891, CalPortland Company's first operations began in Colton, Calif., with a cement plant that supplied cement for the erection of the Hoover Dam. The company is also famous for the "Colton Liberty Flag" on top of Mount Slover, which was first raised in 1917 and at the time was one of only three locations in the U.S. permitted to fly the flag at night (the other two places that were permitted to fly the American flag from sunrise to sunrise were over the National Capital and in Frederick, Md., over the grave of Francis Scott Key, composer of the National Anthem). The 38-by-24-foot flag served as a landmark for decades on Interstate 10 until 2013, when the flag was permanently retired due to new mining activities on the mountain. The flag now resides at the San Bernardino County Museum.
Today, CalPortland Company is a major diversified building materials and construction solutions provider to the western United States and Canada, but its roots remain at the Colton site. Although the cement plant operations in Colton were idled after the economic downturn in 2009, the aggregate operations have significantly increased in recent years in response to a pickup in the marketplace, according to Chad Warren, regional aggregates manager for southern California. And with that increase in market activity came the need to invest in quality equipment that could meet the company's demands for flexibility, mobility and high production.
PRODUCTIVITY AND FLEXIBILITY
CalPortland's Colton site is comprised of three primary materials, which include limestone, schist and a granitic-type rock, Warren said, as well as varying amounts of fines that come with the natural materials on site. The diversity in material made it necessary to select equipment that was not only highly productive, but flexible in application as well.
"All of our materials have their various characteristics that make them either conducive or difficult to process," he said. "Some tend to make more dust than others; others are more abrasive. It's an everyday challenge to keep the right blend of those materials in the plant, so we had to make sure that we could adjust to the changing conditions of the materials. It was critical for us to select equipment that would allow us to make adjustments on the fly to maintain our production capacity and not force our operators into performing a lot of manual labor."
Already familiar with KPI-JCI and Astec Mobile Screens thanks to a successful wash plant purchase in 2007, CalPortland chose to consider the manufacturer once again as it sought to invest in a spread of equipment that could meet their production goals of up to two million tons per year of material for local ready-mix operations and the local construction market.
"When it came time to select the additional equipment for the increase in production operations on site, it made sense to look at KPI-JCI and Astec Mobile Screens," Warren said. "They provided the full range of equipment – from crushing and screening to washing and conveying – that was necessary to get us to the production that we needed."
Not only did KPI-JCI and Astec Mobile Screens provide a complete line of equipment to choose from, but the equipment also proved capable in processing the diverse material on site, Warren said.
"The limestone typically is not as hard to crush as the granite or the schist, but with the durability and robust nature of KPI-JCI and Astec Mobile Screens' jaw crusher and the K400+ cone crushers, we are able to process these materials as we need to, rather than allowing the materials to dictate what we're able to do," he said.
Ryan Dahlke, sales representative for Goodfellow Corporation, worked with CalPortland to select the proper spread of equipment, and said flexibility was the main concern for the setup.
"They needed a lot of flexibility due to the different types of material that they're going to get into," Dahlke said. "With this plant design, with whatever types of material they get into, they're able to make adjustments, either by swinging off a radial stacker to make base, or shoot material up to make product for asphalt as well."
Today, CalPortland utilizes an extensive spread of equipment, including a CS3055 portable jaw plant, 6203 scalping screen, two 8203LP screens, two Kodiak® Plus K400+ Cone Crushers, six 36" x 100' radial stackers, a 42" x 12' VGF Feeder, an FT4250CC Horizontal Shaft Impact Crusher, FT300DF cone crushing plant and an FT3055 jaw crushing plant.
"One of the main differences that I've noticed in working with the KPI-JCI and Astec Mobile Screens equipment is that it's built very robust. It's built for quarry operations and it's built to take the day in and day out abuse. There are no corners cut on trying to make something lighter. From what I've seen, everything's built stout and able to handle whatever we throw at it."
NO CORNERS CUT
Although the first equipment CalPortland's Colton operation purchased was stationary, the company quickly followed up with track-mounted equipment that could be moved around the site. CalPortland chose to remain with the same manufacturer it had previously found success with to save time and money in stocking parts, training crew members and hauling material.
"Once we selected the CS3055 jaw crusher for our primary plant, bringing aboard the FT3055 trackmounted unit was just a natural choice," Warren said. "Through our research, we found that there is no difference between the units- there were no corners cut on the track-mounted unit. This compatibility saves us from having to stock different parts and training maintenance crews to do two different procedures when working on the equipment."
By investing in the same track-mounted version of the new primary plant, CalPortland was also capable of moving the crusher around the site and save a "tremendous amount of money on hauling," Warren said. The company also saw up to a 30 percent increase in production by replacing its old equipment with the new crushing plant and were able to process larger rocks in the crusher.
In addition to its FT3055, the company is also utilizing an FT4250CC horizontal shaft impactor to crush asphalt grindings for the asphalt plant on site at the Colton facility. By recycling the asphalt grindings, the company is able to recapture a product that otherwise would be thrown away and incorporate that back into the asphalt mix, ultimately saving money, producing a superior product and helping the environment.
"We were utilizing a different brand before, and once we brought the FT4250 on site, the production capacity for our recycled asphalt product increased immensely and the maintenance and repair on the unit is half of what the other unit was," Warren said. "Blow bar changes can now be done in half a day, whereas before it was taking a full day. That makes a huge difference when your margins are as tight as ours."
CalPortland also saw significant improvement when it replaced its older equipment with an FT300DF cone crusher to make base material. By introducing the FT300DF cone crusher to the site along with the FT3055 jaw crusher, the company saw an instant increase in production, Warren said. "We were able to increase our production by at least another 50 to 70 tons per hour over what we had been using, and we got our work done in a quicker period of time," he said. "It was also a lot less maintenance for my personnel to keep that plant ready to run every day. When you operate a facility for more than 100 years, you're going to have piles of material that weren't put there in the best of conditions. The track-mounted equipment will allow us to deal with the variability in this material and process it as quickly and efficiently as we can and turn it into a viable product."
Although Warren had never used a roller bearing crusher before his purchase of the K400+ cone crushers and the FT300DF, he says he's been "very pleased" with the experience so far.
"If you ask 25 people, they're all going to give you their own opinions, so I was curious to experience the roller bearing design for myself," Warren said. "And so far, with about 100,000 tons through the two K400+ cone crushers, I've been very pleased with the experience. We put a number down on paper that we wanted to hit, and we've exceeded that number on all levels of production."
"These Kodiak Plus crushers are able to just take it all and keep going. You can walk right next to one running at full capacity and have a normal conversation. It's nice and smooth and quiet- you don't hear a lot of chaos going on in the crusher, and that gives me the confidence that these crushers are going to last and I'm not going to be forced to put a lot of man hours into them."
Find Astec product availability nearby
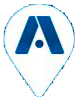