How to Contain Asphalt Plant Noise
Production of hot mix asphalt generates a variety of noise and a range of noise levels from the plant and from movement of trucks and loaders. But technological advancements in the design of asphalt mix production equipment have significantly reduced sound levels emanating from a plant.
In fact, noise is not the dominant issue within a community when a contractor is seeking approval for construction of a new plant or expansion of an existing facility. According to Catherine Sutton-Choate, Astec Inc. director of environmental compliance and product documentation, odor and traffic are the two most common concerns of a community.
“Noise isn’t the biggest problem, because every community has a sound ordinance,” Sutton-Choate says. “Every county or city or in some cases state has a very clearly defined noise ordinance dictating what a plant can or cannot do based on the sound and the time of day. Either you comply or you don’t. A plant would not be allowed to operate if it didn’t comply with the ordinance.”
She says that more important today is if the plant is going to be a “good neighbor” and fit in with the community.
“Years ago, plant after plant was put up in the middle of nowhere, so many of the concerns plants face today weren’t an issue. Most people think if a plant isn’t near residential homeowners there won’t be a problem with permitting, but where that might have been true years ago, it’s no longer the case. These plants are going to be near someone who doesn’t want them there,” Sutton-Choate says.
“How well that plant is going to integrate with its surroundings is significantly more important than it was 20 years ago. The idea that a plant is out of sight, out of mind is not true anymore because no matter where you have the plant, it’s going to be near other local uses. Our industry has to understand the plant has to be able to fit into the community,” Sutton-Choate says.
But because HMA plants do generate noise, contractors need to be proactive and do what they can to make sure noise levels at the property line comply with applicable ordinances. She says that when contractors are looking to construct a new plant or expand or update an existing facility, they rely on modeling software to determine what the sound levels of the plant will be.
“We put in the sound levels of the components the plant will likely install and we model it so see what the sound levels of the plant will be once it’s operational,” she says. “If the model shows the plant will exceed the levels in the sound ordinance, plant operators have a number of recourses to attenuate the sound to bring the plant into compliance.”
HOW TO REDUCE THE IMPACT OF PLANT NOISE
Noise at an asphalt plant is generated from a variety of sources and is defined as incoherent sound -- two or more sounds that do not possess a common frequency component. Because these noise sounds are from various aspects of the plant, no single noise control solution can reduce sounds from all noise components.
Following are the plant components that are the greatest contributors to the overall noise level of the plant, along with some component-specific solutions. By reducing the noise level of each component, plant operators can take a big step forward to complying with a noise ordinance and being a good neighbor.
Burner Assembly
A major source of noise at some asphalt plants is from the burner assembly of open-fired burners. Noise results from the combustion process and from the burner blowers, which are fan-type arrangements with a variety of motor drives. The sound level is a function of burner type, fuel, mixing, pressure, and heat release. However, most facilities in the U.S. now use total-air burners, which are quiet because the burner is completely enclosed once mounted on the drum (see below). A silencer is often a standard part of the design as well for modern burners.
REMEDY: The drum itself generally acts as a partial enclosure, but to suppress extreme open-fired burner noise, the flame should be totally enclosed, using a heavy construction with thick acoustical insulation. Seal all air paths to the flame and install a silencer with good low-frequency attenuation on the outside air intake. When a fan-type burner blower is used, enclose and insulate the blower if it is not made with a heavy material, such as steel. Further reduce noise by installing a dissipative silencer on the air intake and by surrounding the blower's drive with an insulated barrier or enclosure.
Exhaust Fan
The exhaust fan on the baghouse generates a continuous, steady, broadband noise (sound distributed over a large frequency range), and the impeller blades create their own sound. This noise is transmitted through the fan’s casing, adding to the noise from the fan's drive system, including shafts, belts, sheaves, bearings and motors.
REMEDY: Fan noise can be reduced in two ways: by installing a silencer on the exhaust stack and by enclosing and installing acoustical insulation on the fan casing. Two silencer types are available. With a reactive silencer, the tuned frequency must match the impeller blades’ tone. If a dissipative silencer is used, the broadband noise is reduced as is some of the impeller noise. Another treatment is to shield the fan's drive using some type of barrier but note that a barrier around the entire fan assembly will make access more difficult.
Drive Systems
Asphalt mixing plants utilize many different drive systems, all of which contribute to the noise generated by the plant. Whether the system is drum, drag or pugmill, all components create noise.
REMEDY: Efforts to reduce or contain the noise from drive systems could vary depending on the drive system, but the following principles are effective on any drive system.
The sound level of a drive’s motor is continuous and steady and depends on the motor’s type and size, so it’s difficult to actually reduce the noise. But to contain it, block the motor from view using either a barrier wall or an enclosure. If you opt for an enclosure, make sure the area is ventilated to prevent overheating of the motor and install a silencer to permit airflow and to prevent motor noise from exiting through the ventilation. Insulate the motor acoustically, not thermally, and mount it on isolators to help prevent the noise from radiating through the equipment frame.
Another noise producer within the drive system is the reducer, which generates continuous and steady tones, corresponding to the rotation of the individual reduction stages. The sound level is a function of the reducer's type and size as well as a function of the tolerances and loading of the reducer's teeth. As with the motor, contain reducer noise using a barrier or enclosure, but note that overheating of the reducer may be a concern. Also, mount the reducer on isolators because the noise that it generates originates from casing vibration. Noise from the motor’s chain drive results from contact by the metal chain to other metal components, including sprockets, guards, and guides. Shielding chain contact locations from view using either a barrier or enclosure will help contain chain noise. Acoustical insulation also is beneficial.
Air Compressor
Used to perform a variety of functions throughout the plant, the air compressor generates noise by the intake and discharge fans and by the rotation of the air compressor and its motor.
REMEDY: To reduce air compressor noise, use an insulated enclosure, and install outside air intake and discharge dissipative silencers. Vibration isolators might also be needed if the air compressor's mount results in a structure-borne sound problem. Noise also can result from rigid pipe connections, so don’t overlook them when working to control air compressor noise.
Dust Blower
This compressor-type unit generates broadband noise associated with the blower's rotation and drive system. The resulting noise is continuous, steady and a function of the blower's type and size.
REMEDY: Enclose the dust blower's assembly, including the pressure relief valve, and install silencers on the air intake and discharge. Isolate the blower’s mount and any rigid pipe connections.
Air Cylinder
Used to move a gate or chute, an air cylinder makes gas-flow noise when air is expelled from it.
REMEDY: Install a diffusive silencer at an air cylinder's exhaust. Additional noise suppression can be achieved by installing a dissipative silencer in combination with the diffusive one.
Vibrator
Noise is generated by a vibrator as it’s used to maintain material flow through the cold feed bins and the intake chute on the drum.
REMEDY: Isolate the vibrator from the plant's frame or any other large metal part without affecting its intended function. If the vibrator does come in contact with a large metal part, shield that part from view using a barrier or enclosure.
Aggregate
Aggregate noise is generated when aggregate passing through the shaker screen is directed to the conveyor or rejected and when aggregate strikes the interior of the metal drum during the veiling process.
REMEDY. To suppress shaker screen noise, install soft liners to create buffers between the aggregate and the metal. If additional suppression is needed, install a barrier or enclosure. To reduce drum noise, insulate and enclose the drum. (Astec’s Double Barrel® drum, where the outer shell acts as the insulated enclosure, accomplishes this.)
Generator
Noise from a generator powering an HMA plant might be more noticeable than noise from the plant’s components.
REMEDY. Consult with the generator manufacturer about the best way to contain the noise. Most generator manufacturers offer special packages that include silencers to help curb the noise level.
Trucks
HMA plants generate a significant amount of truck traffic, which can create noise issues.
REMEDY: Only one of the solutions – planning the plant site to restrict or eliminate truck backup to eliminate the use of the backup beeper – is in the hands of the plant. The other truck-related noise issues – tailgate slamming, revving the engine, and Jake braking – are the responsibility of the truck operator, but plants can work to educate truck operators to help reduce noise issues. A no-idling policy for all equipment on site, plant loaders and delivery trucks can also help.
INVOLVE THE COMMUNITY
When constructing, expanding, or even upgrading a hot mix plant, Sutton-Choate says it’s essential to involve the community in the process.
“They need to reach out to the community members early in the process and get a sense of what their concerns are because people are scared of what they don’t understand and people in our industry need to understand that – education goes a long way. This applies whether putting in a new plant or upgrading or expanding an existing plant,” Sutton-Choate says.
“Address the issues right up front. Here’s how we’re going to comply with the sound ordinance. Are we going to smell it? Probably, but here’s what we’re going to do to mitigate that and the fact is you might not smell it very much at all.
“Part of what has to happen right up front – for a plant that wants to be a good neighbor – is to find out what the potential neighbors’ concerns are and then explain how their concerns are going to be addressed. Customers that don’t do this aren’t going to get a permit.”
Sutton-Choate says the “smart contractor” meets with the planning board and gets information about the community where they want to locate the plant, then finds out the long-term goals of the community.
“Make sure a hot mix plant is going to be compatible with those long-term goals, because if the plan is to put in all these residential communities in the area you want to locate, a hot mix plant in the middle of it is going to be problematic at best.”
She recommends the contractor host an informational meeting, bringing in subject matter experts who can talk about anything that comes up. “It’s much more effective when you do this in advance rather than wait to address the concerns in a hearing,” she says.
Sutton-Choate adds that if a plant is going to be producing warm mix asphalt, they should emphasize that early in the process. “If you’re producing WMA, play that up because there are so many benefits to the community and WMA lessens the impact of the plant,” she says. “Lower mix temperatures generate less asphalt fumes, which results in lower odor emissions from the plant. If you’re making WMA, commit to making as much as possible as often as possible.”
PLANT AESTHETICS TO FIT IN
Sutton-Choate says a big part of being a good neighbor is making sure the plant’s aesthetics are acceptable to the community. She says most communities have very specific requirements covering signage, fencing, and even landscaping including trees, grass, shrubs, and flowers.
“That’s because the biggest concern of the community is how is installation of a facility going to affect my property value, because no one wants to live next to an asphalt plant,” she says. “When a plant does a good job of trying to maintain the aesthetic nature of the facility in line with the community where its located, that plant doesn’t have a significant impact on the value of surrounding property.
“If a contractor tries to be a good neighbor and maintains aesthetic compatibility with the surrounding property, maintains the plant and the site and ̶ most importantly maintains the equipment ̶ it’s going to give the community less reason not to want them there.”
Find Astec product availability nearby
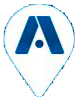