Combatting the unpredictable JT-Effect with inline heater solutions
Highlights
The Joule-Thomson Effect, also referred to as the JT effect, can negatively affect natural gas production if not accounted for. Increasing the temperature with an inline heater can counter the JT effect.
To get natural gas from a wellhead to your home, business, or plant for practical use, gas is processed and transported through interstate and intrastate pipelines at high pressure.
Compressing the gas allows for more volume to be transported more quickly. Pressures can reach up to 1500 pounds per square inch (psi). To put that in perspective, your local distribution company (utility company), which delivers the gas to homes and businesses, moves natural gas at around 3 psi or lower.
The point at which a utility company draws gas from the interstate or intrastate pipeline is often referred to as a citygate. Here, gas is decompressed to lower the pressure for residential distribution. Power generation plants and other large industrial facilities will typically pull directly from the interstate or intrastate pipelines, but also need to reduce the pressure before using the gas.
Decompressing (throttling) natural gas causes a reduction in the temperature of the gas. This phenomenon is known as the Joule-Thomson (JT) Effect. If the temperature reaches below freezing, water molecules in the gas will form hydrates, which could build up and create blockages. Valves, regulators, and other pieces of equipment will also freeze and cause major problems.
One common method to counter the JT Effect is to increase the temperature of the gas before it is decompressed. This is done with an inline heater. There are a few different options for inline heaters, including bath heaters or a thermal fluid heater with heat exchanger combination. They can be fired heaters or electric.
Bath Heaters
A typical process bath heater consists of a shell that contains a fire tube and a process heating bundle. A burner is mounted on one end of the firetube, which doubles back to an exhaust stack. The shell is filled with a solution of water-glycol, molten salt, or oil, which is heated by the firetube.
Carefully controlled heat is introduced into the firetube, transferring heat into the bath solution. The heated solution heats the process bundle and the fuel gas flows through it without contamination.
The water bath process is great for applications where materials cannot accept direct heat. Since the water bath circulates around materials in the firetube, sensitive materials that cannot be heated directly will choose the indirect heating method. You see water bath heaters used primarily in the processing of oil and natural gas for safe, effective regulation of pressure and treatment of the materials. The process is also used to prevent fluid damage and material coking.
Water bath heaters create consistent heat in a relatively simple process and typically cost less initially than other heating systems. The heaters don’t typically need a pump or control valve to operate and can even be built to operate with a generator, using solar power or without electricity at all.
The primary advantage of these units, beyond protecting the product from direct heat, is the ability to allow for very tight temperature control over a wide range of flow rates.
However, water bath heaters are typically not a good choice for heating materials that need extremely high temperatures as the natural convection that occurs is not efficient. For the water bath process to work economically for your application, you need to have the right material and the volume. Because the heating method is based on natural convection, the flux rates tend to be lower and the units can be quite large in size and very expensive for too large of an application. Bath heater sizes range from about 0.5 to 15 million Btu/hour.
Thermal Fluid Heaters + Heat Exchangers
A typical thermal fluid heater consists of a shell that contains a helical coil. A burner is mounted on one end of the shell and fires through the helical coil. The burner heats the coil directly with its hot gases, which double back to an exhaust stack. Thermal fluid, (water-glycol) is pumped through the coil and carries the heat to the heating tubes inside a nearby heat exchanger.
The fuel gas flows through the shell of the heat exchanger where it is heated by its heating tubes. The thermal fluid circulates continuously through the heater and heat exchanger tubes.
Thermal fluid heaters range from 0.5 million to 80 million Btu/hour and the thermal efficiency of a thermal fluid heater is usually about 15 percent higher than a bath heater. The higher efficiency results in significantly less fuel usage. The thermal fluid heater system also uses less liquid and has faster fluid velocity than a bath heater. Consequently, reaction time is faster and provides better temperature control. And there is less liquid to maintain.
Compared to a water bath heater, thermal fluid systems are closed and rarely require additions of fluid. An electric heater is also a closed system, but unlike the other two, it doesn’t require any thermal fluid.
A combination thermal fluid heater and heat exchanger has many important advantages over a bath heater:
Higher thermal efficiency
Lower emissions
Lower liquid volume
Faster reaction time
Better temperature control
Easier to maintain
Longer heater life
Closed system eliminates frequent refilling
Making the Right Choice
While there are a lot of factors to consider when choosing a heater, the good news is you don’t have to make the decision alone. Astec partners with companies to help them achieve their heating needs.
Astec engineers will ask what you’re heating, how much of it and how fast you want it heated. From there, they will recommend a heating process that will work for your product, and your budget.
It is important to select a heater that does not compromise production and increase operations costs. Conducting a cost-benefit analysis based on your needs will ensure you will get the most out of the heating system and do so in the most efficient way possible.
Find Astec product availability nearby
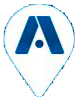