Astec Technology Helps to Reduce Waste in Wastewater
The City of Phoenixville partners with SoMax + Astec to become the first plant in the U.S. to use hydrothermal carbonization to treat their wastewater
Highlights
Country / Region | Pennsylvania, USA |
---|---|
Installation Site | City of Phoenixville |
End User | SoMax Circular Solutions |
Application | Hydrothermal carbonization (HTC) for wastewater treatment |
Equipment | Heatec HCS thermal oil system |
Fuel Type | Natural gas and electricity |
You may not realize it, but a lot goes into treating our wastewater. These multimillion-dollar facilities work around the clock to manage waste, process the material, and filter it for various re-use. What’s leftover once the waste is processed is a mix of material that the facility is left to manage, and the industry has been working hard to find better, healthier and more sustainable ways.
SoMax, a waste solutions company, has worked for over 10 years to revitalize a process called hydrothermal carbonization (HTC). Their technology treats waste in an innovative and groundbreaking way that eliminates harmful pharmaceuticals, plastics, and toxins from organic waste. The conversion process yields clean, carbon-based fuel, fossil-free fertilizers, and nutrient-rich water.
Out With The Old
In the United States alone, we produce 15,000 wet tons of human waste per day and the standard way of processing waste leaves just that, a lot of waste, all of which still has a lot of value and energy left in it in the form of hydrogen, carbon and more.
And so technology has been in development to find ways to keep the good elements from our waste to harness its energy while removing the harmful chemicals we ingest as humans
One such technology, Hydrothermal carbonization (HTC), also known as subcritical water or hot compressed water carbonization, was first identified in 1913 and was revitalized with research conducted by Villanova University funded through Dan Spracklin and the SoMax team.
Spracklin became the CEO of Gray Brothers Septic Services in 2013 and one of the first things he noticed was the magnitude of organic waste in the local area. With his company, Spracklin saw the need to do something with this waste and to find a more sustainable solution for waste treatment and approached his local wastewater treatment plant in Phoenixville, PA with an idea to incorporate HTC into their facility.
“We had worked with Phoenixville, having a 50 year relationship with them with the Gray Brothers business, and they were making plans for a multimillion dollar upgrade to the roof of the digester at their facility,” SoMax CEO Dan Spracklin said. “Their old system was very inefficient, not creating any additional energy for them and the HTC system intrigued them enough that we began a feasibility study.”
The city began a three-year permitting process and became the first large-scale HTC system of its kind in the United States that transforms biosolids into hydrochar, a coal-like substance that can be used to generate energy to power its facility. In fact, when at capacity and integrated with a cogeneration system, it is expected to produce enough hydrochar to generate a surplus of electricity.
What is HTC?
Hydrochar? HTC? What are these and what do they have to do with Astec?
Phoenixville’s HTC system, the first large-scale system of its kind in the United States, transforms biosolids into hydrochar which is a coal-like substance.
“HTC is a chemical thermal chemical process. And it's all in the name. So it's Hydro meaning wet and thermal, meaning we add heat to it,” Spracklin said. “The easiest way to think about it is an industrial sized pressure cooker and any organic material you put in will go under chemical changes and transformation. In this case, we're putting sewage sludge in it and then we're transforming it by doing a couple of things.
“One is we're killing off all the bacteria, all the pathogens, all the viruses that are in wastewater. We're also destroying pharmaceuticals, microplastics and forever chemicals in this process. We take it from an unsanitary product that typically gets land applied, or landfill or incinerated and that typically municipalities will pay to get rid of and we turn that into a product that can actually be used.”
The end product that can be used is Hydrochar.
“With the SoMax technology, we're taking something that's a waste and a cost to dispose of for this municipality of sewage sludge and turning it into an energy dense product,” Spracklin continues. “This is done through a process called gasification where you heat up the material to a high temperature and in a lack of oxygen, it converts into gas. So it'll convert into methane, carbon monoxide, hydrogen and CO2 and then that goes through what's called a genset.
So it's like an internal combustion engine that will create heat and electricity.”
Engineering Prowess for a New Industry & Application
Since early 2023, the HTC process has been running alongside anaerobic digesters at Phoenixville to do just that - with the help of Astec’s Heatec HCS heaters.
The SoMax team contacted Astec during the installation process in Phoenixville with the need for reliable and consistent heat at the location that could produce efficient thermal oil at 500° Farenheit where it is used during the last phase of the heating.
“The fabricators we were talking to that were helping to build our reactors had also built asphalt plants,” Spracklin said. “They told us to reach out to Astec and they came with a reputation of quality products and delivery.”
The Heatec HCS heater is needed for the final stage of heating to get the material up into the reaction temperature range, which is between 180° Celsius and 20° Celsius.
“We target 200° Celsius for sewage sludge,” Spracklin said. “First we do an energy recovery step through a heat exchanger, bring it up to about 150° Celsius and then the Heatec HCS heater skid takes over and feeds oil in our heater skid and brings it up to that 205° Celsius.”
The Heatec HCS system also has been so efficient for Phoenixville that they are consuming less energy than initially projected.
“Right now we're consuming about half an MMBtu (one million British thermal units) which is about eight bucks per hour to transform all this material,” Spracklin said. “Originally, when we had designed this, the engineers said we would be at one and a half MMBtu of energy consumption. The Heatec HCS system has been so efficient that we're basically only using about a third of the projected energy that's needed.”
Another advantage for SoMax of Astec’s Heatec HCS thermal oil system is that it runs both on natural gas and electricity.
“On certain projects that we're working on, natural gas is not available and so being able to run on electricity is fantastic, Spracklin said. “For some of our customers who are coming to us because they're cost conscious and they want environmental solutional, that we can run on renewable energy for the Heatec HCS system and remove any fossil fuel consumption in our process whatsoever is great.”
With the Astec partnership happening so seamlessly in Phoenixville, SoMax is already looking to expand upon the partnership with another project in the works in Tennessee as Astec can help engineer solutions from the ground up for facilities as they look to capitalize on this groundbreaking solution.
“I can tell you right now, Astec’s Heatec HCS thermal oil system has worked fantastically, exactly as specified exactly as promised," Spracklin said. “We have not had any issues with it whatsoever. There's a quality aspect to working with them and their reputation precedes themselves.”
Eventually in Phoenixville, they hope to use its hydrochar for cogeneration. The treatment plant has used biogas for heating only. The hydrochar can be heated and gasified, and the gas then can fuel a generator. Phoenixville expects to produce enough hydrochar to generate 153% of the treatment plant’s energy demand, which would mean selling a lot of power back to the utility grid.
Find Astec product availability nearby
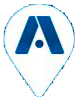