The Million Yard Maintenance Plan
Outback Materials trusts in the experience of the Astec team for extensive repairs on their workhorse concrete plant for the California High-Speed Rail project
Highlights
The Workhorse CON-E-CO AllPro 12 CM
Outback’s CON-E-CO ALL-PRO® 12CM plant is configured to charge both Concrete Mixer Trucks and End-Dump transfers for delivery of concrete to the project sites. The Central Mix Concrete Batch is based around the aggregate and cement core module. The overhead aggregate bin, cement silo’s and water weigh batcher bolt onto the core section of the plant. The mixer legs bolt into the front of the plant reducing the seismic design loads.
The ALL-PRO 12CM flexible configuration allowed the producer to lay out the central mix plant and drive over grizzly in an area 14′-0 X 150′-0″. The site design allows for a future material handling system to be added as required by future production demands.
This plant expands Outback’s current Ready-mixed concrete market area to the west of Fresno. By incorporating the CON-E-CO 12-yard tilt mixer, Outback can provide increased quality control and production for the High-Speed Rail concrete mixes.
Products
When your company purchases a new piece of equipment, at some level you expect to enjoy many years of hassle-free operation. With an extensive capital purchase like a concrete plant, crews often operate season after season without needing to worry too much about how the plant is operating, especially when it is performing well for you.
No matter how much of a workhorse any machine is, regular maintenance is the key to ensuring long-lasting success. The team at Outback Materials knows that having the right experience to help with those processes is incredibly important.
“We bought our new CON-E-CO ALL-PRO 12 CM in 2016, and when you have a new plant, it doesn't take a whole lot of specialized knowledge to keep it running smoothly,” Jordan Lovett, Operations Manager at Outback Materials said. “However, as time goes on, and parts get replaced and fixed, the configuration of the plant begins to change. After running significant yardage through the plant, we wanted to make sure we gave the plant the upgrades it needed, and that some of our future repairs conformed to best practices.”
Their plant, which was installed to provide concrete for the numerous over-passes and bridges along the California High-Speed Rail project in Fresno and Madera counties, had run nearly 1 million cubic yards through it when they started to experience heavy vibration and other issues.
“The vibration on the platform was getting so bad that major components on the plant were actually breaking and we didn't really know exactly what to do to fix the problem,” Lovett said. “We looked at the pinion gears and the thrust rollers, and started to talk with our dealer about what could be causing the issues.”
Scott Humphrey with DHE Noble worked with Lovett and his team for seven months to troubleshoot the issues before recommending that the team of experts at Astec come to the site for a complete plant inspection.
“Our team talked to Paul Kratky at Astec for a few months, going through the issues we were having,” Lovett said. “He would answer our calls at all hours of the day and eventually we all agreed it was best to have him come and work directly with us.”
Complete Trust Comes from Experience
The Astec team of experts spends years working with their equipment and customers. This not only means they know the product inside and out, it also means they are going to work with each plant location to provide the customer with the best options for their specific issues. This was important to the team at Outback as they wanted to make sure their plant was not only running at peak performance but would also continue to do so with proper upgrades and repairs.
“Major repairs come around so infrequently that when it’s time to perform them, you want to have a resource you can consult before you start replacing critical plant components,” Lovett said. “After nearly a million yards through the plant, the repairs we needed to perform were manpower intensive and required some pretty expensive parts – and if your only practice doing these repairs is once every five to seven years, you’re probably not going to do a great job unless you have someone who can walk you through it in advance.”
“Ultimately, our decision to talk to Paul was the right one. After completing the recommended repairs, a lot of the vibration on the plant went away,” Lovett continues. “It was good to have him there to point us in the right direction when we went to actually make these repairs.”
Setting the Stage for Future Success
Not only did the Astec team offer their perspective on what repairs were needed, their experience also allowed for the Outback team to receive the training necessary to ensure the plant continued to operate smoothly after repairs were made.
“Although we were following the manufacturer’s preventative maintenance program, Paul was able to give us a customized PM schedule based on what he saw during his inspection,” Lovett said. “In addition, he provided us with some specially machined parts that conformed to the wear patterns on the plant. We wouldn’t have gotten them if he hadn’t come out for his inspection.”
The variable frequency drive (VFD) for a mixer changes the motor output when a plant isn’t actually batching load, contributing to major power savings when used properly. The Astec team was able to identify the fact that the excessive vibration damaged the VFD and recommended moving the VFD to prevent any future damage to the expensive component.
“Paul recommended that we relocate our electrical box to ground level or at least move it off the main platform where it was getting so much heavy vibration,” Lovett said. “He told us the VFD wasn't going to last if we kept it where it was. We're in the process of replacing the VFD now and moving it based on his recommendation.””
Since the inspection from the Astec team, the Central Mix Concrete Batch Plant has not experienced any further breakdowns.
“There were a lot of repairs that we had to do just because of routine wear and tear,” Lovett said. “If we didn't do them at the right time, we would probably have run into some bigger problems. Paul definitely helped us get the plant in a better place through these preventative repairs that were completed in the right time frame.”
Find Astec product availability nearby
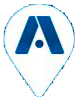