Putting People First Wins Kokosing National Safety Award
When you make safety a priority, your people will always keep it top of mind. Instead of working around a task that might be unsafe, employees that have been trained to put safety first will always seek another solution.
At Kokosing Materials Inc. (KMI), Fredericktown, OH, team members are expected to speak up and stop an unsafe task.
“At Kokosing, we truly believe one incident is too many,” Jerry Estep, terminal manager at Kokosing says. “Commitment to Safety is first in our company Core Values and we are continuously looking at all of our processes to make sure they fit these core safety values. We rely on input from all team members. Those with one day of experience to long-term members of 35+ years. A long believed idea handed down from the founder of our company.”
So when team members expressed the hazards when distributing hot asphalt cement on a job site, the KMI team sought a solution to improve the process.
Handling hot liquid asphalt is a task we’ve all dealt with, but not one we necessarily enjoy. The standard way in the 90’s to distribute this material was to hold a hose by hand while the liquid was flowing into the kettle.
“Years ago we improved the process by adding a 90° elbow and a piece of pipe that could be put onto the kettle and secured in various ways,” Estep says. “This greatly improved the process by moving the team member back from the end of the hose during the fill process.”
Next, KMI installed quick-connecting couplers to the lids of their company-owned Kettles to help ensure a secure connection while also removing team members from the point-of-entry area.
“This seemed to improve the process, but presented a problem for our customers who did not have the ability to make these modifications,” Estep says. “This forced the customer to turn to other suppliers to fulfill their needs. All of these process improvements reduced many hazards associated with the task however, the potential risk of our team members to be in the line of fire of unseen dangers still existed (plugs in a hose, pumps at full speed under pressure, pumps being used in reverse and bypassing the pressure relief valves).”
So KMI was still seeking another solution to further refine the process and turned to their partners at Astec Industries for help.
“After seeing additional safety issues with this process and being aware that there must be change to ensure team member safety, we contacted Astec and shared our concerns,” Estep says. “We presented our ideas on ways to engineer out the hazards for a safe loading system and Astec fine-tuned it.”
A Safe Step Forward
The team at Astec immediately agreed the system could be safer and their engineers worked with KMI to come up with a solution they both could agree on.
“We felt adding a variable speed drive would help control the flow,” Estep says. “Being able to start slowly, to verify the movement of product was essential to identifying hazards before it’s too late, as in a plugged line during cold mornings.”
They also wanted to add heat tracing and insulation to the upright standpipe on the output side of the pump to ensure that heat was being transferred to the first swivel in the piping. Estep says this helps reduce the chances of a plugged line. They also moved the controls and E-Stop from the main electric panel, out closer to where the operator has immediate control of the machine.
“We worked with the electrical engineering team and talked them through the changes KMI wanted to see,” Steve Munson, Director – AC Storage & Blending Systems at Astec Industries says. “We discussed making a pump skid with a spring assist loading arm and controlling the pump with a VFD and a dead man switch. They bought the first unit and liked it so much they decided to purchase five more.”
And all of this happened because KMI knew they could count on Astec to help fix any issues they had.
“That’s the relationship we share,” Estep says. “Astec is always right there for our operators night and day. Our industry is challenging, working all hours, lots of moving parts that we rely on. When things are not working out, help is readily available.
“We work on the same level of commitment and understanding of our needs and the needs of our team members,” Estep continues. “This is a relationship that has been built over many years and both companies are open-minded to new innovations.”
Award-Winning Safety
The stationary, hot oil heated, hard-lined, swivel spout kettle with PLC controls that was designed by KMI and Astec allowed employees to lower the spout into the tar kettle with very little effort, ensuring residual AC is cleared out of the equipment preventing buildup in the lines. This innovative spring-assisted system also helps prevent muscle strains.
The innovation gained national recognition from the National Asphalt Pavement Association who awarded KMI with the 2021 Asphalt Operations Safety Innovation Award at their annual meeting in Phoenix this year. The Asphalt Operations Safety Innovation Award recognizes the development and implementation of innovative ideas that lead to improved worker safety in a roadway work zone, plant site, or quarry environment, and companies whose safety practices go above and beyond industry standards.
"Are we proud of this achievement? Yes, we are very proud! But our comment to safety isn’t about winning awards. It’s about the well-being of our team, of our families, of our communities,” Estep says. “It is important to us that everyone, in any industry, goes home to their family every day, the same way you came to work. We are proud of our safety culture, and we are always working towards improving. It is our hope that everybody involved in our industry would have the same mindset of safety every hour of every day."
That’s the relationship we share. Astec is always right there for our operators night and day. Our industry is challenging, working all hours, lots of moving parts that we rely on. When things are not working out, help is readily available. We work on the same level of commitment and understanding of our needs and the needs of our people. This is a relationship that has been built over many years and both companies are open-minded to new innovations.
”Find Astec product availability nearby
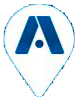