Permission Granted
California company meets environmental requirements with Astec plant. DeSilva Gates chose industry-leader Astec and its Double Barrel® plant for its Sunol location.
Highlights
Country / Region | USA |
---|---|
Installation Site | Sunol, California |
End User | DeSilva Gates |
Application | Asphalt Mixing |
Drum | 500 TPH (454 MTPH), 9 ft x 47 ft (2.74 m x 14.33 m) Astec Double Barrel® dryer/mixer with warm mix system |
Burner | Phoenix Talon |
Baghouse | 95,893 CFM Pulse Jet baghouse |
Storage | Six 300-ton (272 tonne) New Generation Storage System Silos |
Environmental Controls | Astec 36,000 CFM Blue Smoke Collection System with a fiberbed filter V-Pac™ Stack Temperature Control System with v-flights and variable frequency drive |
Products
In addition to sunshine, California is known for having the largest, tallest, and oldest trees in the United States—and some of the most stringent air quality standards in the nation. Doing business in California requires patience and careful planning to complete the environmental impact process and acquire the correct air quality permits for asphalt plant operations.
DeSilva Gates knows this process firsthand.
INDUSTRY-LEADER ALIGNED
In early 2015, DeSilva Gates completed installation of its first Astec asphalt plant at its Sunol, California, location. According to Alan French, general manager of DeSilva Gates Aggregates, a division of DeSilva Gates Construction, the company looked to Astec as the leader in the industry to provide the latest technologies to meet the requirements for an asphalt plant in the State of California and Alameda County.
“The Sunol asphalt plant was three-plus years in the making. We aligned ourselves with Astec, the industry leader for hot- and warm-mix asphalt equipment technology, support, and training,” said French. “We are now positioned to move forward and provide asphalt, in addition to aggregates, from this location, supporting our customers and construction division in and around the area.”
UNIQUE DESIGN
DeSilva Gates installed a 500 TPH (454 MTPH), 9 ft x 47 ft (2.74 m x 14.33 m) Astec Double Barrel® plant. The Double Barrel®v drum mixer is designed to produce quality mixes while keeping the operating costs per ton of mix low. Its design meets the environmental codes, even in a stringent state like California. The entire drum is used for production of RAP (reclaimed asphalt pavement) up to 50 percent.
The California Department of Transportation (Caltrans) determines the amount of RAP that can be used in various mixes for projects around the state. For DeSilva Gates, having the ability to use a high percentage of RAP prepares the company for future changes to Caltrans’ mix specifications.
“We are running up to 40 percent RAP in our mixes per CalTrans specs,” said French.
INNOVATIVE TECHNOLOGIES
DeSilva Gates’ asphalt plant is equipped with Astec’s warm mix system, which uses a multi-nozzle manifold to produce a foamed warm-mix asphalt that is odorless and smokeless.
Another Astec technology incorporated into the DeSilva Gates’ plant is the patented V-Pac™ Stack Temperature Control System. This system allows the operator to set an optimum stack temperature for a particular mix. For example, the V-Pac lowers the stack temperature on high-RAP mixes, open-graded mixes, and SMA (stone-matrix asphalt); the stack temperature is raised on virgin mixes and low-RAP mixes. The V-Pac makes it possible to run SMA and high-RAP mixes back-to-back with virgin mixes without flight adjustments.
The V-Pac system has “v-flights,” unique drum flights with a deep v-shape, and variable frequency drives (VFDs), which provide control of the drum rotational speed. V-flights create uniformity of the aggregate veil during the drying process, which results in better heat transfer, a reduction of fuel use, increased productivity, and longer bag life.
STATE-OF-THE-ART ASPHALT PLANT
“Our Sunol location has the most state-of-the-art asphalt plant compared to any place, not just in California, due to the air quality standards we’ve had to meet,” shared French. “We also had to meet the local seismic design requirements as directed by the building code in Alameda County.”
French continued: “Our Sunol facility has been working day and night since about May or June (2015) and we’ve currently run more than 100,000 tons (110,231 tonnes) through the plant. The plant is still new, and after a few more months of operating, we’ll feel more comfortable with the Astec plant and its state-of-the-art technologies. We’re working up to running 500 TPH (454 MTPH) and we’ll get there soon. Right now, the Sunol plant is permitted for 1,000,000 tons (1,102,311 tonnes) of asphalt per year.
When the process to install an asphalt plant began, I believed Astec and its technologies and advancements were the best fit for our company. We’re pleased so far and look forward to a rewarding relationship with Astec.”
Find Astec product availability nearby
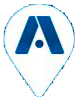