Mining for More
A unique partnership between the University of Minnesota and Dakota Aggregates has led to the mining of the last large aggregate reserve in the Minneapolis metropolitan area.
The origins of the site can be traced back to the early 1940s, when the U.S. government seized 12,000 acres of Minnesota farm land to build a munitions plant during World War II. Before the factory could be completed, the war ended, leaving the government without a use for the land that sits in the center of Dakota County, which is about 20 minutes south of the Minneapolis/St. Paul metro area.
Shortly thereafter, the government deeded nearly 7,700 acres of the land to the University of Minnesota for agricultural research purposes. In 2000, the University created a property management plan that would eventually become the 5,000-acre University of Minnesota Outreach, Research and Education (UMore) Park.
In preparation for UMore Park, the university completed an inventory describing the land use and resources. It also conducted an assessment that determined about 360 million tons of high-quality sand and gravel existed on the property.
“The university, knowing it was sitting on a rich deposit of aggregates, started researching uses for the aggregates and determined there was a need for aggregates in the metropolitan area,” said Stacey Hannover, operations manager for Dakota Aggregates.
With that in mind, Dakota Aggregates was established in 2013 with the specific purpose of mining the 1,600 acres available at UMore Park. The new company worked closely with Road Machinery & Supplies, an authorized dealer for Astec, to obtain a spread of equipment that would allow them to meet the growing demands of their customers.
Today, Dakota Aggregates utilizes a wide variety of equipment from Astec, including twin 7’ x 20’ screen plants, a triple-deck 7’ x 20’ screen, a Kodiak® Plus K200+ closed-circuit crushing plant, two PTSC2618 Vari Vibe® high frequency screens, and a custom-engineered wash plant. The company also recently added the new 2056 Pioneer Jaw Crusher to its equipment line-up, which has increased throughput by 20 percent, while at the same time improving particle shape and reducing downtime, Hannover said.
OPTIMUM PERFORMANCE
From April to November, Dakota Aggregates runs 20 hours a day, five days a week, and produces a variety of products, including concrete aggregates, bituminous aggregates and top soil products. In 2015, the company produced more than a million tons of material for the local markets. Concrete aggregates are used for ready-mix plants in the south-metro area in southern Minnesota, whereas the bituminous aggregates feed an on-site asphalt plant, which serves a 60-mile radius from the UMore site, Hannover said.
The process of mining UMore Park begins with the twin 7’ x 20’ screen plants at the north mine site de-sanding the material. The rock is then fed to the 2056 Pioneer Jaw Crusher, screened via the triple-deck 7’ x 20’ screen to the K200+ crushing plant, sized again, and then, if necessary, finished through the wash plant.
Hannover first began considering adding the 2056 Pioneer Jaw Crusher to his crushing circuit once the company began mining at full depth and realized it needed a jaw crusher on site to size the material and better utilize the K200+ cone crusher.
“We’re scalping at the face of the mine at about eight inches, so we really needed a nice-sized jaw crusher to handle that eight-inch size material crushing down to a 2 ½-inch size,” Hannover said. “The 2056 was a really good fit for us. We have a better sized, more uniform feed now, and that’s really helping the cone crusher perform to its optimum ability.”
The 2056 Pioneer Jaw Crusher is a newly-designed, more compact model that features a 20” by 56” jaw crusher that is ideal for all crushing applications. The small gap provides an excellent nip angle at a tight closed-side-setting, making it a perfect fit for applications where material is minus-16”, according to Tim Harms, product manager for Astec.
Significant changes engineered into the new 2056 model include a new single cylinder auto-tension system, which offers less maintenance, increased reliability and reduced wear part consumption, Harms said. The crusher’s new wear seat provides easy access and increased uptime, while a new corrugated stationary wedge increases the crusher gap and maintains a steep nip angle, providing less slippage, lowering the wear costs by providing longer jaw die life. Its unique flywheel retention system secures the flywheel in place, providing unmatched reliability and longevity.
For Hannover, the top three features that drew him to the new 2056 Pioneer Jaw Crusher were the ease of adjustment, the portability and the accessibility.
“Years ago, to adjust a jaw crusher, it would take you half an hour to an hour adjusting the crusher,” he said. “Now, with the remote adjust, one operator can adjust it from a keyboard and you’re not exposed to the dangers, you’re outside of the crusher, it’s fantastic. You shut down and in a matter of minutes you’re adjusted to where you want to be and you’re back up and running.”
“That’s a huge cost savings,” he continued. “In this business, downtime is everything. If you’re down even 10 minutes to adjust a jaw crusher, that’s lost production, and that all factors in your cost per ton.”
Portability also proved important during the purchase process, Hannover said.
“It was important to us to be able to back the jaw crusher right into our operation,” Hannover said. “We purchased an electric crusher on a portable chassis, so it was simple to back it into place, plug it in and get right to work.”
So far, Hannover has run the plant more than 1,000 hours, and has experienced no downtime with very little wear so far.
“The reliability on the 2056 Pioneer Jaw has been fantastic,” Hannover said. “We’ve had zero downtime in 1,000 hours, and that’s huge.”
GROWTH AND EXPANSION
Looking to the future, Dakota Aggregates plans on investing in a higher-horsepower Kodiak® Plus Cone Crusher to achieve even more throughput, allowing it to meet the growing demands of its customers. It’s the support and reliability Hannover has received that gives him confidence to grow the operation and expand into new markets, he said.
“We know that RMS and Astec will be there with us to help us in every aspect of our processing needs,” Hannover said. “With a factory located right in South Dakota that offers professional training, we’re constantly taking advantage of their educational support and educating our employees in all aspects of crushing and screening. Our employees come back with great knowledge, and excited about how they can help improve performance. It’s time and money well spent.”
“Time and again, they deliver on their promise of hands-on serviceability. They’re there when we call them. And that’s important to us.”
Find Astec product availability nearby
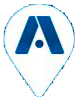